TM 5-3895-382-24
Prior to checking the vibratory system, drive the machine
backwards and forwards several times operating the propel
controls in all speed ranges. While the machine is being driven
backwards and forwards, check the condition of the rubber
blocks. The blocks act as an isolator between vibrating and
non-vibrating parts of the machine.
Check for the sound of the relief valves opening. The opening
pressures of the relief valves are given in Relief Valve
Pressure Tests in Testing And Adjusting.
Problem: Low charge pressure.
Probable Cause:
1.
Low oil level in hydraulic oil tank.
2.
Restricted hydraulic filter element.
3.
Failure of the steering pump.
4.
Charge relief valve adjustment not correct.
5.
Failure of the servo control assembly.
6.
Failure of the vibratory control solenoid valve.
7.
Main relief valve setting is not correct or valve does not
close.
8.
Pump port plate wear causing excessive leakage from
the high pressure line into the pump housing.
Problem: Vibratory does not work in high or low
amplitude.
Probable Cause:
1.
Low charge pressure.
2.
Failure of the vibratory pump.
3.
Faulty vibratory control switch on the console.
4.
Faulty vibratory selector switch on the console.
5.
Electrical problem with EDC (If Equipped) or the wiring
to the EDC.
Problem: Periodic loss of vibratory in high or low
amplitude.
Probable Cause:
1.
Faulty vibratory control switch.
2.
Faulty vibratory selector switch.
3.
Loose connection in the electric circuit wiring.
Problem: Harsh engagement of vibratory.
Probable Cause:
1.
Charge circuit relief valve is set too high.
Problem: Slow vibratory stopping.
Probable Cause:
1.
Relief valve pressure set too low.
2.
Main relief valve does not close correctly on the return
side of the closed loop circuit.
Problem: Compactor will not reach maximum vibratory
frequency.
Probable Cause:
1.
Drum oil level is too high.
2.
Engine high idle is not correctly adjusted.
3.
Frequency gauge (if equipped) is defective or not
correctly adjusted.
4.
Low charge pressure.
5.
Incorrect internal stops in servo.
6.
Vibratory system pressure higher than main relief valve
pressure.
7.
Excessive pump/motor internal leakage.
8.
Failure of the O-rings for the servo piston assembly.
9.
Incorrect voltage at the EDC on machines equipped with
variable frequency.
10.
Failure of the EDC.
11.
EDC neutral setting incorrect.
Problem: Variation in maximum frequency readings
between high and low amplitude.
Probable Cause:
1.
Incorrect neutral adjustment of the pump servo control
assembly.
2.
Mechanical failure of the pump servo control assembly.
3.
Main relief valve setting is not correct or valve does not
close correctly on one side of the loop line.
4.
Failure of the pump swashplate assembly.
13-31
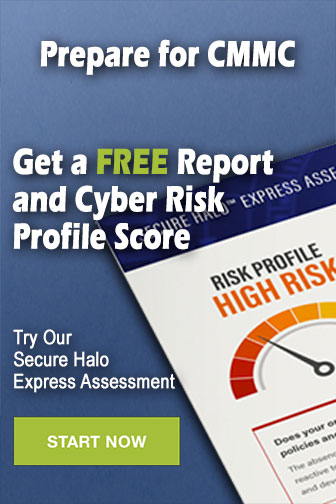