TM 5-3895-382-24
When current is applied to cause the armature to move
towards magnet (13) a torque shift occurs at pivot (14). That
torque shift causes the flapper to move closer to nozzle (16).
As the flapper moves closer to the nozzle, the pressure rises
between nozzle (16) and orifice (20). This pressure increase
causes the oil to flow through control port 1 (21).
Initially, due to step input from the control current, the flapper
closes off the nozzle sending all oil through the control port
causing the pump to go to full stroke. As the oil pressure rises
in the passageway between the nozzle and the orifice, it
moves the flapper back toward the null position. When the
torque output of the torque motor stage and the pressure
feedback are equal, the pilot control system is then equalized.
When the pilot control system is equalized, the flapper is in the
position to maintain the desired speed setting. The control oil
pressure in passage (21) is then proportional to the control
current plus the control oil pressure in the passage (23).
The second stage of the EDC routes the control oil pressure
from passage (21) to one end of actuator spool (6). When the
control oil pressure reaches 85 kPa (12 psi) it overcomes
modulation spring (7) and shifts the actuator spool. When the
spool shifts it moves rotary valve cam (5), which rotates rotary
valve (3). The rotation of the rotary valve opens a port and
allows charge oil to pass to the servo piston. Oil acting upon
the servo piston causes it to shift and rotate the swashplate on
its axis.
A valve sleeve that is concentric with the rotary valve is
attached to the swashplate. When the rotary valve rotates and
opens a port the swashplate turns. The valve sleeve turns with
the swashplate and closes off the port, shutting off the supply
of control oil. Because the sleeve valve moves with the
swashplate, the swashplate is able to follow the rotational input
of the rotary valve.
The modulator spring tension setting is designed to give a
specific actuator spool deadband width and is not adjustable.
Null adjust screw and locknut (4) moves the fixed deadband in
relation to its alignment to the rotary valve control port opening.
Manual override lever (2) on the PCP allows the pump to be
controlled manually instead of electrically. The manual
override lever actuates the PCP flapper valve.
13-27
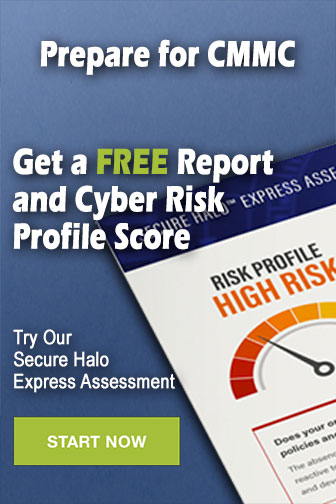