TM 5-3895-382-24
Testing and Adjusting
Troubleshooting
During a diagnosis of the hydraulic system, remember that
correct oil flow and pressure are necessary for correct
operation. The output of the pump (oil flow)
increases with an increase in engine speed (rpm) and
decreases when engine speed (rpm) is decreased. Oil
pressure is caused by resistance to the flow of oil.
The 4C-4892 ORFS Fittings Group can be used to make
pressure tests on the vibratory system. Before any tests are
made, visually inspect the complete hydraulic system for
leakage of oil and for parts that are damaged. For some of the
tests a magnet and a mm (in) measuring rule are usable tools.
When any test is made of the vibratory system, the hydraulic
oil must be at the normal temperature for operation (38C
[100F]).
Sudden movement of the machine or release of oil under
pressure can cause injury to persons on or near the
machine. To prevent possible injury, do the procedure
that follows before testing and adjusting the vibratory
system.
1.
Move the machine to a smooth horizontal location.
Move away from working machines and personnel.
2.
Permit only one operator on the machine. Keep all
other personnel either away from the machine or in view
of the operator.
3.
Activate the parking brake.
4.
Stop the engine.
5.
Move the hydraulic control lever to all positions to
release any pressure in the hydraulic system.
6.
Carefully loosen the filler cap on the hydraulic oil tank.
7.
Make sure all hydraulic pressure is released before any
fitting, hose or component is loosened, tightened,
removed or adjusted.
Visual Checks
A visual inspection of the vibratory system and its components
is the first step when a diagnosis of a problem is made. Then
check the operation of the machine. Finally, check the
vibratory system with gauges. Perform the following
inspections.
Do not check for leaks with your hands. Pin hole (very
small) leaks can result in a high velocity oil stream that
will be invisible close to the hose. This oil can penetrate
the skin and cause personal injury. Use cardboard or
paper to locate pin hole leaks.
1.
Check the oil level of the hydraulic oil tank.
2.
Look for air in the oil that is in the hydraulic oil tank. Do
this immediately after the machine is stopped. Use a
clear bottle or container to get a sample of the oil. Look
for air bubbles in the oil that is in the bottle.
3.
Check all oil lines, hoses and connections for leaks and
damage. Look for oil on the ground under the machine.
4.
Remove and check the hydraulic filter element for
foreign materials.
a.
Bronze-colored particles give an indication of pump
port plate failure.
b.
Shiny steel particles give an indication of pump or
motor piston failure or motor cam deterioration.
c.
Rubber particles give an indication of a seal or hose
failure.
d.
Aluminum particles give an indication of steering
pump failure.
Checks During Operation
With the engine running, operate the machine in each direction
and from low to high speed. Make note of all noises that are
not normal and find their sources. If the operation is not
correct, refer to the list of problems and probable causes.
The checks during operation can be used to find leakage in the
system. They can also be used to find a bad valve, pump or
motor. Vibratory frequency can be used to check the condition
of the vibratory motor and the Pump.
13-30
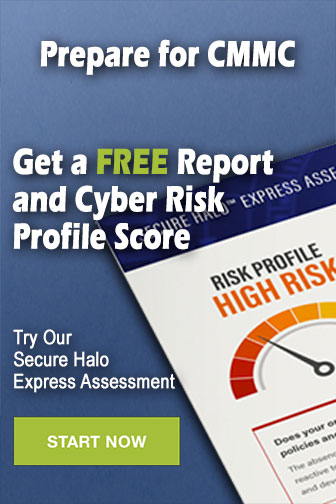