TM 5-3895-382-24
Servo Piston Assembly/Electrical Displacement Control (EDC)
EDC.
(1) Electrical Displacement Control (EDC). (2) Sensing piston. (3) Spring. (4) EDC neutral adjustment. (5) Servo piston neutral adjustment.
(6) Servo control piston. (7) Feedback linkage. (8) Displacement control spool. (9) Control oil passages. (10) Pressure control pilot (PCP) valve.
(11) Manual EDC override.
Electrical displacement control (1) is mounted on the hydraulic
pump.
The pump control consists of three sections: EDC (1),
displacement control spool (8), and servo control piston (6).
EDC (1) is a two-stage electrohydraulic control. uses feedback
linkage (7) and control oil (9) from the steering system pump to
set up a closed swashplate control circuit. EDC (1) receives
electrical input from the flow analyzer flow control dial at
pressure control pilot (PCP) valve (10).
EDC (1), uses an electrohydraulic pressure control pilot to
control differential pilot pressure. PCP (10) converts an
electrical input signal to a hydraulic input signal to operate
spring (3) centered sensing piston (2). Sensing piston (2) is
mechanically linked with the displacement control spool (8)
through feedback linkage (7). As sensing piston (2) moves,
displacement control spool (8) is moved. This opens a path for
control oil (9) to move servo control piston (6). Servo control
piston
(6)
tilts
the
swashplate,
varying
the
pump's
displacement.
As sensing piston (2) moves to the left as shown, displacement
control spool (8) is moved to the right.
This opens a path for control oil (9) to servo control piston (6).
As servo control piston (6) tilts the swashplate, feedback
linkage (7) moves sensing piston (2) through spring (3)
connection back towards neutral to maintain the swashplate
angle set by PCP (10).
EDC (1) maintains the position of the swashplate in proportion
to the electrical input. Servo control piston (6) has feedback
linkage (7), which moves the displacement control spool (8) in
the proper relation to the input signal and the position of the
swashplate. Any swashplate position error is sensed by the
feedback linkage (7), and displacement control spool (8)
corrects the error.
13-14
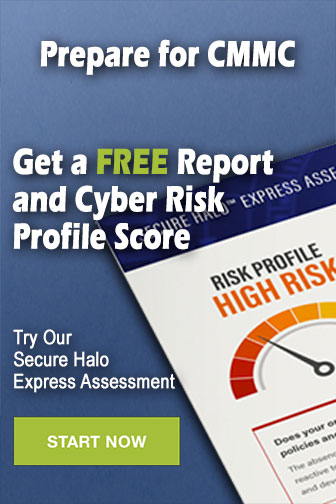