TM 5-3895-382-24
Vibratory Pump.
(12) Closed circuit loop line port. (15) Closed circuit loop lines port.
(16) High pressure relief valve (High amplitude). (17) Charge oil inlet.
Vibrato Pump.
(18) Charge relief valve. (19) High pressure relief valve (Low
amplitude).
The vibratory pump contains charge relief valve (18) and high
pressure relief valves (16) and (19), one for the high amplitude
side of the closed loop circuit and one for the low amplitude
side of the closed loop circuit. Both the charge relief valve and
high pressure relief valves are of the direct acting type.
Vibratory Pump Schematic.
(12) Closed circuit loop line port. (15) Closed circuit loop line port
(16) High pressure relief valve (High amplitude). (17) Charge oil inlet.
(18) Charge relief valve. (19) High pressure relief valve (Low
amplitude). (21) Check valves. (22) Case drain oil line.
Charge oil enters the vibratory pump through charge oil inlet
(17). The charge pressure entering the vibratory pump is
controlled by the charge relief valve in the vibratory flushing
valve. The charge relief valve (18) located inside the vibratory
pump is used to prevent damage to the pump. An orifice in the
vibratory pump charge relief valve (18) allows approximately
1.5 gallons per minute of oil to flow through the pump case for
cooling. If the charge pressure entering the pump reaches
2869 kPa (415 psi), charge relief valve (18)
opens to allow more oil to flow through case drain oil line (22)
to the hydraulic tank.
The maximum working pressure for each dosed circuit loop
line is limited to 18 980 kPa (2755 psi) above charge pressure
by high pressure relief valves (16) and (19). Check valves (21)
are built into the high pressure relief valves. The primary
purpose of the check valves is to keep closed circuit loop lines
(12) and (15) full of oil, to make up for internal leakage and
protect the charge system from high pressure oil when the
vibratory system is in operation.
Servo Piston Assembly
Servo Piston Assembly.
(1) Lever. (2) Piston. (3) Adjustment screw. (4) Cavity. (5) Cavity.
The pump swashplate is moved by the servo piston assembly.
The servo piston is a double-acting piston that is a par of the
vibratory pump. The swashplate is connected to the center of
the piston with lever (1).
The electrical displacement control is a solenoid operated,
three position valve that has two coils. The electrical
displacement control sends the flow of charge oil to the servo
piston assembly. Orifices are installed in the passage that
connect the electrical displacement control to the servo piston
assembly. The orifices are used to control the rate at which
the servo piston assembly stokes and destrokes.
13-9
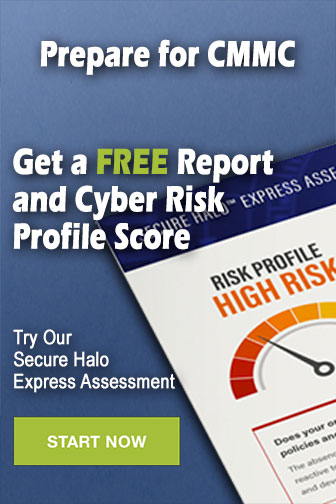