TM 5-3895-382-24
Illustration 100
Locations for measuring the bore runout of the flywheel housing.
(1) Bottom
(2) Right side
(3) Top
(4) Left side
1.
Fasten the magnetic base of the dial Indicator group to
the crankshaft flange. Adjust the contact of the dial
indicator in order to touch the bore of the flywheel
housing at location (1). Set the pointer of the dial
indicator to 0.0 mm (0.00 inch).
2.
Push the crankshaft to the rear in order to remove the
main bearing clearance before the measurement is
taken at each location.
3.
Turn the crankshaft. Record the dial indicator reading at
locations (2), (3), and (4).
4.
Calculate
the
difference
between
the
lowest
measurement and the highest measurement of the four
locations. This difference must not be greater than 0.30
mm (0.012 inch). This dimension is the maximum
permissible distance for the bore runout of the flywheel
housing.
Flywheel Checks
Face Runout Check
Illustration 101
Tooling setup for measuring the face runout of the flywheel.
1.
Install the dial indicator in Illustration 101, as shown.
Push the crankshaft to the rear in order to remove the
main bearing clearance before the measurement is
taken at each location. Set the pointer of the dial
indicator to 0.00 mm (0.000 inch).
2.
Turn the flywheel. Read the dial indicator for every 90
degrees.
3.
Alignment error.
NOTE:
For a complete description of Type 1 and Type 2
engines, refer to the Systems Operation, Testing
and Adjusting Module, "Engine Design" for more
information.
a.
Type 1 and 9RM Engines
Calculate
the
difference
between
the
lowest
measurement and the highest measurement of the
four locations. This difference must not be greater
than 0.20 mm (0.008 inch). This dimension is the
maximum permissible distance for the face runout of
the flywheel.
6-97
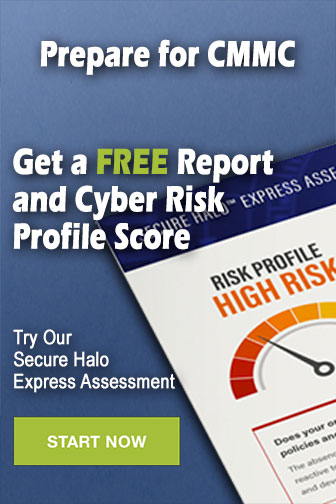