TM 5-3895-383-24
Charge oil is supplied by the charge pump (11). Charge pump
(11) is an internal gerotor pump, which is integral to the pump
(1). Charge oil flows to charge filter (4) through line (13).
Charge oil flows through charge filter (4) before entering the
vibratory circuit. The filtered oil enters the vibratory circuit
trough the charge pressure line (3).
Charge oil fills the closed circuit loop lines (12) and (17) across
the makeup function of high pressure relief valves (8) and (9).
The charge pressure in both closed circuit loop lines (12) and
(17) is equal when the vibratory system is off.
Charge oil flows through pilot oil passages (14) and (19). The
spool is held in neutral by the springs. Oil flow is blocked to
the flushing relief valve (5).
The charge pressure oil is controlled by the leakage of the
closed loop and the charge relief valve (10). Charge pressure
is measured after the charge filter. Charge pressure (neutral)
is 3000 150 kPa (435 22 psi). Refer to the Testing and
Adjusting module for the testing procedures.
When the vibratory system is not active, excess charge oil
passes through pump (1). The return oil flows into the return
manifold through the lines (20).
Return oil and normal internal leakage oil from both the propel
and the vibratory circuits flow to the return manifold. The
thermal bypass valve is integral to the return manifold. The
thermal bypass valve directs the return oil through the oil
cooler or the thermal bypass valve directs the oil to the
hydraulic oil tank (16). This is dependent on oil temperature.
The thermal bypass valve allows 13 L/min (4 US gpm)
of hydraulic oil to flow through the oil cooler at
temperatures that are below 65C (149F). The
remainder of the oil flows to the hydraulic oil tank (16).
The thermal bypass valve begins to direct some
hydraulic oil to the oil cooler above to 65C (149F).
The remainder of the oil flows to the hydraulic oil tank
(16).
The thermal bypass valve directs all of the hydraulic oil
to the oil cooler at 70C (158F).
11-18
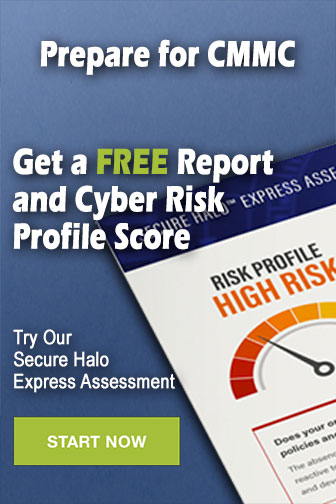