TM 5-3895-383-24
Hydraulic oil from the pump (1) flows through the closed circuit
loop line (12) to motor (6). The high pressure side and the low
pressure side of the closed circuit loop lines (12) and (17) are
shown in illustration (2). The oil flows to the motor and the
motor becomes the high pressure side of the closed circuit.
Resistance of the motor to the flow will create high pressure.
The high pressure oil drives motor (6).
Low pressure oil from the motor (6) flows back to the pump (1)
through line (17). Line (17) will become the low pressure side
of the closed circuit.
The high pressure relief valve (9) will limit the maximum
working pressure of the closed circuit loop line (12) to 35000
kPa (5076 psi) above the low pressure. When the system
pressure in line (12) becomes greater than the high pressure
relief valve setting, oil will dump into the closed circuit loop line
(17). The closed circuit loop line (17) is the low pressure side
of the closed circuit. The high pressure oil will dump into the
closed circuit loop line (17). This will relieve the high pressure
side of the closed circuit.
The high pressure oil from the dosed circuit loop line (12) will
flow through the pilot oil passage (14). This will shift the
shuttle spool inside the flushing valve (18). This position is
shown in illustration (2). Low pressure oil from the closed
circuit loop line (17) flows through the flushing valve (18) to the
flushing relief valve (5). Low pressure oil dumps over the
flushing relief valve (5) to the flush motor (6). Flushing relief
valve (5) is set lower than the relief pressure of the charge
relief valve (10) in pump (1). This allows the motor to be
flushed with the low pressure oil during vibratory system
operation.
The return oil from pump (1) and motor (6) flow through line
(20) to the return manifold. The thermal bypass valve is
integral to the return manifold. The thermal bypass valve will
direct the return oil through the oil cooler. The thermal bypass
valve will also direct the return oil to the hydraulic oil tank (16).
This depends on oil temperature.
The thermal bypass valve allows 13 L/min (4 US gpm)
of hydraulic oil to flow through the oil cooler at
temperatures that are below 65C (149F). The
remainder of the oil flows to the hydraulic oil tank (16).
The thermal bypass valve begins to direct some
hydraulic oil to the oil cooler at temperatures above
65C (149F). The remainder of the oil flows to the
hydraulic oil tank (16).
The thermal bypass valve directs all of the hydraulic oil
to the oil cooler at 70C (158F).
When the oil pressure in the closed circuit loop line (17) drops
below pressure of the charge circuit oil, the charge circuit will
replenish the closed circuit with makeup oil. The closed circuit
is replenished across the makeup function of the high pressure
relief valve (9). The charge circuit oil replenishes loss from
both the flushing valve (18) and from the internal leakage of
pump (1).
11-20
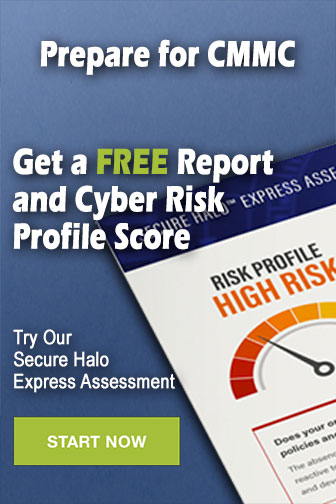