TM 5-3895-382-24
Tightening Procedure For Gearbox Spanner Nut
Measuring Rolling Torque
(A) Torque wrench. (B) Direction of pull. (C) Viewed standing here.
1.
Install seal (1), boot (2), and bearing cone (3) in hub (9).
Install spindle (8) into hub (9). Hold the spindle
stationary and use a torque wrench as illustrated above
to determine the rolling torque created by the seal and
boot. A typical rolling torque is 3.4 Nm (30 lb-in).
NOTE:
Bearing cones (3) and (4) should be clean and
wiped dry of any lubricating oil. Bearing cones
which have oil present will affect rolling torque
readings.
2.
Heat shaft bearing cone (4) in an oven to 135C
(275F). Press in the shaft bearing cone until the rolling
torque increases 1.7 to 4.5 Nm (15 to 40 lb-in) greater
than the value measure in Step (1).
NOTE:
It will be necessary to continually rotate the
housing to seat the bearing cone in order to
obtain a correct rolling resistance.
3.
Apply 9S3263 Thread Lock to the threads of the locknut.
Install washer (5), lock tanged washer (6) and locknut
(7).
4.
Tighten the locknut with a torque wrench to 306 Nm
(225 lb-ft). Rotate hub (9) to seat the bearing.
5.
Recheck the rolling torque. The final reading should be
1.7 to 4.5 Nm (15 to 40 lb-in) greater than the value
measure in Step (1).
6.
A final rolling torque of 5 to 7 Nm (45 to 65 lb-in) should
result in a bearing preload of .025 to 0.51 mm
(.0010 to .0020 in).
7.
If the lockwasher tang does not line up with the locknut
slot, tighten the locknut to line up the tang and bend into
the locknut slot.
Tighten eight bolts (10) to a torque of .....................20 to 25 Nm
(15 to 20 lb-ft)
NOTE:
Four shoulder bolts (11) are equally spaced.
Tighten four shoulder bolts (11)
to torque of ..................................................................20 to 25 Nm
(15 to 20 lb-ft)
12-10
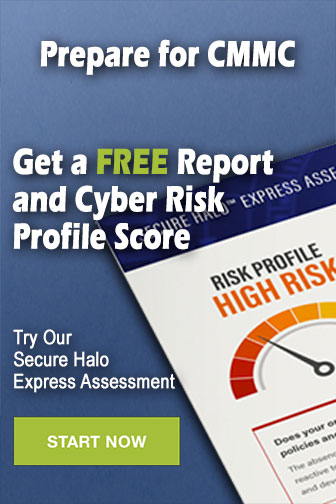