TM 5-3895-383-24
The brake interlock valves (17) and (25) become energized
when the parking brake is pulled up. The brake interlock valve
shifts in order to allow charge oil to go to the drum brake (10)
and the axle brakes (4). The pressure of the charge oil
overcomes the force of the springs and the parking brake is
released.
NOTE:
The description of this circuit flow is only
accurate if the engine is running and the parking
brake is pulled up.
Forward movement of the propel control lever mechanically
moves the directional control valve that is for the axle propel
pump. The directional control valve on the axle propel pump is
mechanically connected to the directional control valve on the
drum propel pump. This allows the two propel pumps to be
synchronized when the propel control lever is moved. This
movement causes charge oil to flow through the bottom of the
servo valves (15). The result is an increase in the angle of the
swashplate of the propel pumps (26) and (19). High pressure
oil flows from the propel pumps (26) and (19) and the oil goes
to each propel motor. Low pressure oil exits the motors and
the oil returns to the propel pumps through return lines (3) and
(11).
Charge check valve (21) closes when high pressure oil is
pumped through the high pressure side of the dosed loop.
Charge check valve (20) opens in order to allow oil from the
charge circuit to enter the return side of the closed loop. This
compensates for internal leakage within the separate circuit
components.
High pressure oil moves the shuttle valve spool that is inside
flushing valve (28). Some of the return oil is forced through the
cases of each motor. This creates a cooling effect. Hot low
pressure oil flows from the flushing valves to the return
manifold and the thermal bypass valve (29). This allows fresh
charge oil to enter the low pressure side of the closed loop
through charge check valves (20).
POR valve (18) and (23) senses the pressure in the high
pressure side of the closed loop. When the pressure in the line
reaches 45000 kPa (6525 psi), the POR valve opens. The
charge oil in lines (9) and (16) returns to the hydraulic tank.
The decrease in pressure in the charge circuit is sensed at the
servo valves. The centering springs in the servo valves
reposition the servo valves in order to reduce the angle of the
swashplate. This effectively reduces the output of the propel
pumps.
Multifunction valves (22) and (27) protect the system from
sudden high pressure spikes. When the system pressure
reaches 48000 kPa (6960 psi) in the high pressure loop, the oil
is routed to the low pressure loop and to the hydraulic oil tank.
During a quick stop or a direction change, this relief valve will
open.
Oil from the case of the propel pumps and the propel motors
flows to the return manifold. Then, the oil is directed to the
thermal bypass valve (29) and the oil flows to the oil cooler or
the hydraulic oil tank.
When the speed selector switch on the control console in the
LOW SPEED position, shift valve (5) is not energized. In this
position, the control piston in each propel motor is open to the
tank. Each propel motor is at the maximum displacement
position.
Reverse Drive Position
The oil flow during the reverse operation of the machine is
similar to the oil flow during the forward operation of the
machine. The directional control valves are mechanically
positioned so that the oil flows through the top portion of the
valve. This will reverse the flow of the oil to the servo valves.
Essentially, the swashplate moves in the opposite direction.
This will reverse the high pressure and return loop lines and
the propel motors will turn in opposite directions. The function
of the other components throughout the propel system operate
in the same manner as the forward operation of the machine.
10-28
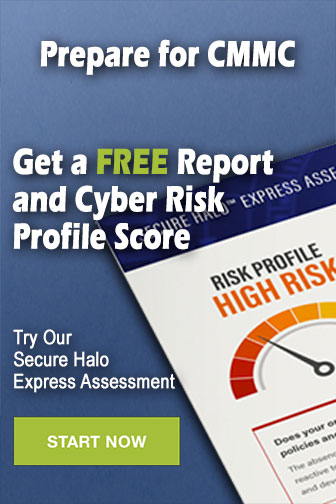