TM 5-3895-382-24
NOTE:
For photographic purposes the pump shown is
out of machine.
3.
Disconnect servo control lines (6) from the axle pump.
Plug and cap the hoses. Install a 3445 kPa (500 psi)
minimum pressure and 9.52 mm (.375 in) or greater I.D.
hose between the two ports where the servo control
lines were connected.
4.
Start and run the engine at low idle.
5.
Look at the 60 000 kPa (8700 psi) pressure gauges.
Both readings, for the axle pump, should be the same
and should be approximately the same as the charge
pressure.
6.
If it is necessary to adjust the neutral position of the
servo piston, remove the protective cap. Loosen the
locknut and turn adjustment screw (5) to get the same
pressure reading on each gauge.
7.
Stop the engine. Remove the 60 000 kPa (8700 psi)
pressure gauges and replace them with 4000 kPa (580
psi) pressure gauges or Tetra gauges.
NOTE:
Using a lower pressure gauge may damage the
gauge.
8.
Start and run the engine at high idle. Engine rpm
should be 2350 50 rpm.
9.
Turn the adjustment screw until both pressure gauge
readings are the same. Then, turn the adjustment
screw clockwise until one of the pressure readings
starts to increase. Note the position of the adjustment
screw.
10.
Now turn the adjustment screw counterclockwise until
the reading on the other pressure gauge begins to
increase. Note the position of the adjustment screw.
Turn the adjustment screw clockwise one-half the
distance to the first adjustment screw position.
11.
Hold the adjustment screw and tighten the locknut to a
torque of 18 to 24 Nm (13 to 18 lb-ft). Install the
protective cap.
12.
Stop the engine. Remove the pressure gauges from the
test ports.
13.
Install the servo control oil lines on the axle pump.
Drum Propel Pump
NOTE:
Do the same procedure for the swashplate neutral
adjustment of the drum propel pump as above
using the drum pump test ports and servos.
11-44
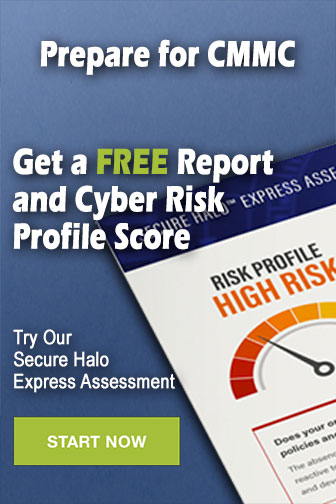