TM 5-3895-382-24
NOTE:
Operate the engine at low idle for a minimum of
five minutes immediately after air has been
removed from the fuel system. Running the
engine for this period of time will help ensure that
the pump is completely free of air. Damage to the
internal parts of the pump which is caused by
metal to metal contact will be prevented.
Adjustment Of Low Idle And High Idle
Illustration 48
Lucas Fuel Injection Pump.
(1) Low idle adjustment screw
(2) High idle adjustment screw
Illustration 49
Stanadyne Fuel Injection Pump.
(1) Low idle adjustment screw
(2) High idle adjustment screw
Work carefully around an engine that is running. Engine
parts that are hot, or parts that are moving, can cause
personal injury.
1.
Low Idle Adjustment
Run the engine until the normal operating temperature
is reached. Check the rpm at low idle. Use the
adjustment screw (1) in order to adjust the low idle.
Loosen the locknut and turn the screw clockwise in
order to increase the rpm. Turn the adjustment screw
counterclockwise in order to decrease the rpm.
NOTE:
The correct rpm for low idle is given in the
following
publications:
Technical
Marketing
Information (TMI) and Fuel Setting And Related
Information Fiche.
2.
High Idle Adjustment
a.
High Idle Adjustment On Type 1 Engines and 9RM
Engines.
NOTE:
For a complete description of Type 1 and Type 2
engines, please refer to the Systems Operation,
Testing and Adjusting Module, "Engine Design"
for more information.
6-61
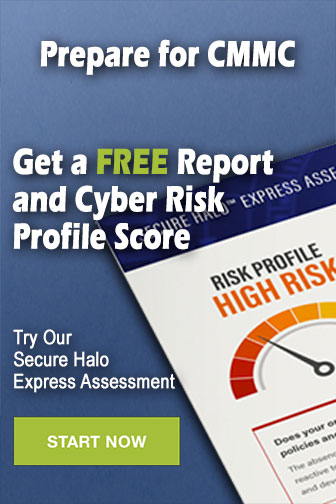