TM 5-3895-383-24
Cleaning the Heavy-Duty Cooling System
Caterpillar Cooling System Cleaners are designed to clean the
system of harmful scale and of corrosion. Caterpillar Cleaners
dissolve
mineral
scale,
corrosion
products,
light
oil
contamination, and sludge. For the recommended service
interval, refer to the Operation and Maintenance Manual
"Maintenance Interval Schedule" for your machine.
Conventional
Coolant/Antifreeze
Cooling
System
Maintenance
SMCS Code: 1350; 1352; 1395
When you initially fill the cooling system with Caterpillar Diesel
Engine Antifreeze/Coolant, it is not necessary to add a
Supplemental Coolant Additive. Caterpillar Diesel Engine
Antifreeze/Coolant already contains supplemental coolant
additive. When you initially fill the cooling system with a
commercial coolant that meets the requirements of "ASTM
D4985",
add
a
supplemental
coolant
additive.
The
supplemental coolant additive in Caterpillar Diesel Engine
Antifreeze/Coolant and in commercial coolants must be
replenished at regular service intervals. See the table for
Supplemental Coolant Additive (SCA) in order to determine the
correct quantity of liquid supplemental coolant additive to use.
S· O·S Coolant Analysis
SMCS Code: 1350; 1352; 1395; 7542
Testing the engine coolant is important to ensure that the
engine is protected from internal cavitation and from corrosion.
The analysis also tests the ability of the coolant to protect the
engine from boiling and from freezing. The SOS Coolant
Analysis can be done at your Caterpillar dealer. Caterpillar
SOS Coolant Analysis is the best way to monitor the
condition of your coolant and your cooling system. SOS
Coolant Analysis is a program that is based on periodic
samples.
NOTICE
Do not use the same vacuum sampling pump for
extracting oil samples that is used for extracting coolant
samples.
A small residue of either type sample may remain in the
pump and may cause a false positive analysis for the
sample being taken.
Always use a designated pump for oil sampling and a
designated pump for coolant sampling.
Failure to do so may cause a false analysis which could
lead to customer and dealer concerns.
New Systems, Refilled Systems, and Converted Systems
Perform a coolant analysis (Level 2) at 500 service hours for
new systems or for converted systems that use ELC or use
DEAC. This 500 hour check will also check for any residual
cleaner that may have contaminated the system.
Recommended Interval for S· O· S Coolant Sample
Table 21
Recommended Interval
Type of Coolant
Level 1
Level 2
DEAC
Every 250 Hours
Yearly
ELC
Not Required
Yearly
S· O·S Coolant Analysis (Level 1)
A coolant analysis (Level 1) is a test of the properties of the
coolant.
The following properties of the coolant are tested:
Glycol Concentration for freeze protection
Ability to protect from erosion and corrosion
pH
Conductivity
Water hardness
Visual analysis
Odor analysis
The results are reported, and appropriate recommendations
are made.
Maintenance Section
Cooling System Specifications
1-30
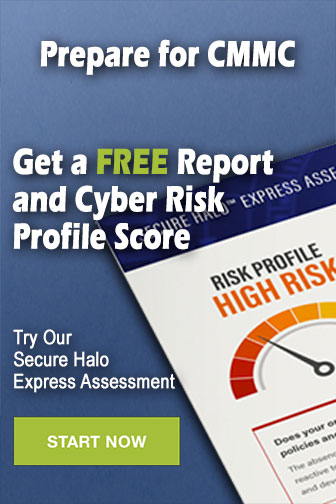