TM 5-3895-382-24
Scheduled Oil Sampling (S· O·S)
Caterpillar recommends using Scheduled Oil Sampling
(SOS), at regularly scheduled intervals, to complement
a good preventive maintenance program.
The Caterpillar Scheduled Oil Sampling Program,
(SOS), was developed to help Caterpillar users realize
the highest possible value from their equipment by
minimizing repair costs and maximizing availability. The
SOS program is a series of diagnostic tests which
analyze used lubricating oils from the oil wetted
compartments of the equipment. By analyzing the used
oils, problems may be identified early, before extensive
component failure occurs. This reduces repair cost and
downtime.
The SOS program is coupled with a wide range of
repair options so that when a problem is identified, an
appropriate matched repair plan is available. This offers
the user a more complete service to minimize repair
costs and schedule down-time. S OS can also
measure the effectiveness of the users maintenance
program.
Obtain SOS Sample
There are several methods used to obtain SOS
samples.
NOTE: Sampling methods recommended are in
preference order. If one of the first two
methods is not feasible, then use the drain
stream method.
Use an in-line sampling valve.
Use a sampling gun inserted into the sump.
Use the drain stream method when changing oil.
When using the drain stream method to obtain an oil
sample, take the sample after some oil has drained out
and before the final drain oil. The oil at the beginning or
end of the drain stream is not mixed well enough to be
representative of circulating oil in the compartment and
may carry debris that can give false S OS analysis
results.
S· O·S Analysis
SOS is composed of three basic tests:
Wear Analysis
Chemical and Physical Tests
Oil Condition Analysis
Wear Analysis monitors the components wear rates by
measuring wear elements and contaminants found in the
used oil. Through monitoring the used oil, normal
component wear trends are determined. Many failures
can be identified when wear trends and/or contaminants
significantly exceed past trends.
Detectable failures are those caused by component
wear and gradual dirt contamination. Wear analysis is
not able to predict failures due to component fatigue,
sudden loss of lubrication, or sudden ingestion of a large
amount of dirt since failures of this nature occur too
rapidly.
Chemical and Physical Tests are used to determine
whether the used oil has been contaminated with water,
fuel or antifreeze and if these contaminants exceed
maximum limits.
Oil Condition Analysis determines the degree of
deterioration of the used oil by measuring the amount of
sulfur products, oxidation, nitration and soot present in
the used oil. It also can monitor additive depletion and
detect ethylene glycol, Dowtherm and butyl cellosolve
contamination.
Oil Condition Analysis can help regulate (reduce,
maintain or extend), oil change intervals for a specific
machine/engine in a given application. Oil Condition
Analysis must always be used with Wear Analysis and
the Chemical and Physical Tests.
S-O-S INTERVAL CHART
Compartment
Interval
Engine Oil
250 Hours
Transmission Oil
500 Hours
Hydraulic Oil
500 Hours
Final Drive Oil
500 Hours
Consult your Caterpillar dealer for complete information
and assistance in establishing a Scheduled Oil Sampling
Program for your equipment.
Maintenance Section
Scheduled Oil Sampling (S· O·S)
1-35
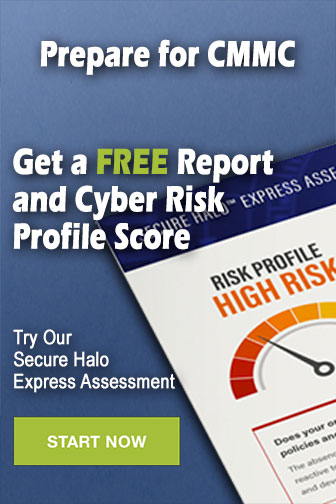