TM 5-3895-383-24
This list of possible problems and possible corrections will only
provide an indication of the location of a problem and the
repairs that are required. Remember that a problem is not
necessarily caused by one part, but by the relation of one part
with other parts. This list can not provide all possible problems
and corrections. Service personnel must find the problem and
the source of the problem. Then, complete the necessary
repairs.
Perform a visual inspection first. If the visual checks are
completed but the problem has not been identified, perform
operational checks. If the problem is not understood, perform
instrument tests. This procedure will help to identify problems
in the leveling blade system.
Hydraulic System Pressure
Release
1.
Move the machine to a smooth horizontal location.
Move away from working machines and personnel.
Stop the engine.
2.
Permit only one operator on the machine. Keep all
other personnel either away from the machine or in view
of the operator.
3.
Move all hydraulic controls to all positions to release any
pressure in the hydraulic system.
4.
Carefully loosen the filler cap on the hydraulic tank to
release any pressure in the tank.
5.
Activate the parking brake.
6.
During certain performance tests it will be necessary to
release the parking brake to help drum movement when
turns are required.
7.
Make sure all hydraulic pressure is released before any
fitting, hose or component is loosened, tightened,
removed or adjusted.
8.
The pressure in the system has now been released and
lines or components can be removed.
Visual Inspection
SMCS Code: 6060-035; 6151-035
Escaping fluid under pressure, even a pinhole size leak,
can penetrate body tissue, causing serious injury, and
possible death. If fluid is injected into your skin, it must
be treated immediately by a doctor familiar with this type
of injury.
Always use a board or cardboard when checking for a
leak.
Personal injury can result from hydraulic oil pressure and
hot oil.
Hydraulic oil pressure can remain in the hydraulic system
after the engine has been stopped. Serious injury can be
caused if this pressure is not released before any service
is done on the hydraulic system.
Make sure all of the attachments have been lowered, oil is
cool before removing any components or lines. Remove
the oil filler cap only when the engine is stopped, and the
filler cap is cool enough to touch with your bare hand.
NOTICE
Care must be taken to ensure that fluids are contained
during performance of inspection, maintenance, testing,
adjusting and repair of the product. Be prepared to collect
the fluid with suitable containers before opening any
compartment or disassembling any component containing
fluids.
Refer to Special Publication, NENG2500, "Caterpillar Tools
and Shop Products Guide" for tools and supplies suitable
to collect and contain fluids on Caterpillar products.
Dispose of all fluids according to local regulations and
mandates.
Perform visual checks first when you are troubleshooting a
problem. Before you make these checks, stop the engine and
apply the parking brake. Shift the propel control lever to the
NEUTRAL position. During these checks, use a magnet to
separate ferrous particles (iron) from nonferrous particles
(O-ring seals, aluminum, bronze, etc.), if necessary.
1.
Check the oil level of the hydraulic oil tank.
2.
Look for air bubbles in the oil or water in the oil
immediately after the machine is stopped. Use a dear
bottle or a container in order to get a sample of the oil.
Refer to Operation and Maintenance Manual, "Lubricant
Viscosities and Refill Capacities" for the recommended
oil grade and the recommended oil viscosity.
a.
Air bubbles may be caused by a fitting that is loose or
damaged. A loose fitting or damaged fitting allows air
to enter the suction side of the system and oil is also
allowed to leak.
3.
Check all oil lines, all hoses, and all connections for
damage and for leaks. Look for oil on the ground under
the machine.
NOTE:
If oil can leak out of a fitting or out of a
connection, air can leak into the system. Air in
the system is as harmful as having too little oil.
13-17
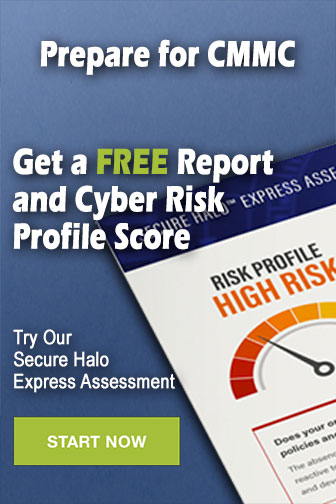