TM 5-3895-382-24
Swashplate angle is determined by how far the propel lever is
moved off center. Due to normal operating force changes, the
swashplates tend to drift from the set position. Drift is sensed
by the feedback linkage connecting the swashplates to the
control valves. This activates the control valves, supplying
pressure to the servo-pistons and maintaining the swashplates
in the set position.
As soon as the swashplates are tilted, the rotating groups
receive the charge oil. The high pressure oil in closed circuit
loop lines goes to each propel motor. The low pressure oil in
closed circuit loop lines leaves each motor and returns to the
pumps, or goes to tank through shuttle valves.
The high pressure oil closes the check valve on the high
pressure side of the closed circuit loop. The low pressure
check valve opens to allow oil from charge circuit oil to enter
low pressure closed circuit loop. This compensates for internal
leakage within the different circuit components.
The high pressure oil in the closed circuit loop moves the
shuttle valve spool inside motor flushing valves (15) and (16).
Hot low pressure oil flows from the flushing valves to the relief
motor shuttle valves. This allows fresh charge oil to enter the
low pressure side of the loop through the pump checks.
The high pressure relief valves protects the system from
sudden high pressure spikes. When the differential pressure is
above the high pressure relief valves setting, the valves route
the oil to the low pressure loop.
Oil from the case of the axle pump goes to the case of the
drum pump, and to hydraulic oil tank (12). Oil from the case of
drum drive motor and axle motor goes to thermal bypass valve
(11).
When the speed selector switch on the operator console is in
the LOW speed position, the speed shift control valve is not
energized. In this position the shift spool in each propel motor
is open to drain. Each motor is at maximum (large)
displacement (low speed).
11-31
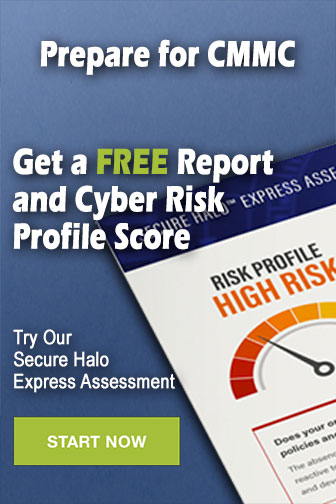