PRINCIPLES OF OPERATIONGENERAL DESCRIPTIONFig. 2. In-Line Engine Model Description, Rotation and Accessory ArrangementFig. 3. 6V Engine Model Description, Rotation and Accessory ArrangementFig. 4. Series 53 Cylinder ArrangementFig. 5. Typical Model and Serial Numbers as Stamped on Cylinder Block (In-Line Engine)Cross Section Views of a Typical In-Line EngineCross Section Views of a Typical 6V-53 EngineFig. 1. Schematic Diagram of Typical Fuel System - In-Line EngineFig. 3. Removing Injector from Cylinder HeadFig. 4. Typical Fuel Strainer and Filter MountingFig. 5. Typical Spin-On Type Fuel Strainer and Fuel Filter MountingFig. 7. Air Intake System Through Blower and Engine (6V-53 Engine)Fig. 8. Light-Duty Oil Bath Air CleanerFig. 10. Air Cleaner Tray (Plugged)Fig. 12. United Specialties Dry Type Air CleanerAir SilencerFigure 14. Typical In-Line Engine Oil Filter MountingFigure 16. Schematic Diagram of Typical In-Line Engine Lubricating SystemFigure 17. Schematic Diagram of Typical 6V Engine Lubricating SystemFigure 18. Typical Cooling System for In-Line EnginesFigure 19. Typical Cooling System for V-Type EngineENGINE COOLING SYSTEM MAINTENANCECooling System CleanersMiscellaneous Cooling System ChecksRaw Water PumpFigure 1. Typical Instrument PanelThrottle ControlFigure 2. Mechanical Shut-Down System Schematically IllustratedAUTOMATIC ELECTRICAL SHUT-DOWN SYSTEMFigure 3. Automatic Electrical Shut-Down System DiagramFigure 5. Alarm System Wiring DiagramELECTRICAL STARTING SYSTEMSFigure 6. Schematic Diagram of Hydrostarter System Showing Oil FlowFigure 7. Hydrostarter Remote Control SystemLUBRICATION AND PREVENTIVE MAINTENANCECold Weather OperationFigure 8. Typical Fluid Starting AidFigure 9. Quick-Start AssemblyPOWER TAKE-OFF ASSEMBLIESTORQMATIC CONVERTERSWARNER MARINE GEARPREPARATION FOR STARTING ENGINE FIRST TIMELubrication FittingsOil PressureAvoid Unnecessary Engine IdlingFig. 1 . Location of Controls on Power Generator SetPREPARING GENERATOR FOR LOADPARALLELINGLUBRICATION AND PREVENTIVE MAINTENANCEPREVENTIVE MAINTENANCEPREVENTIVE MAINTENANCE - ContinuedPREVENTIVE MAINTENANCE - ContinuedPREVENTIVE MAINTENANCE - ContinuedPREVENTIVE MAINTENANCE - ContinuedPREVENTIVE MAINTENANCE - ContinuedPREVENTIVE MAINTENANCE - ContinuedPREVENTIVE MAINTENANCE - ContinuedPREVENTIVE MAINTENANCE - ContinuedTWIN DISC MARINE GEARSPECIFICATIONSSPECIFICATIONS OIL QUALITYCOLD WEATHER OPERATIONSTATEMENT OF POLICY ON FUEL AND LUBRICANT ADDITIVESCOOLANT REQUIREMENTSFig. 2 - Heat Transfer CapacityBulk Inhibitor AdditivesGENERAL RECOMMENDATIONSGENERAL RECOMMENDATIONS - ContinuedENGINE TUNE-UP PROCEDURESEXHAUST VALVE CLEARANCE ADJUSTMENTFOUR VALVE CYLINDER HEADSFig. 3 - Timing Fuel InjectorLIMITING SPEED MECHANICAL GOVERNOR AND INJECTOR RACKPosition Injector Rack Control LeversFig. 6. Governor Spring AssembliesAdjust Idle SpeedFig. 7 Adjusting Buffer ScrewAdjust Governor GapPosition Injector Rack Control LeversFig. 5. Checking Injector Control Rack "Spring"Fig. 7. Governor Spring AssembliesFig. 8. Adjusting Engine Idle SpeedFig. 1. Variable Speed Open Linkage Governor Mounted on EngineAdjusting ScrewsAdjust Maximum No-Load SpeedFig. 7. Adjusting Buffer ScrewFig. 1 - Checking Governor GapInjector Control RackFig. 5 - Locating of Shims and StopsFig. 6 - Adjusting Idle SpeedFig. 8 Adjusting Booster SpringVARIABLE SPEED MECHANICAL GOVERNOR AND INJECTOR RACK CONTROL ADJUSTMENTFig. 3 Positioning No. 3L Injector Rack Control LeverFig. 6 - Location of Shims and StopsFig. 7 - Adjusting Idle SpeedFig. 9 - Adjusting Booster SpringFig. 1 - Engine Load Limit DeviceFig. 4 - Throttle Delay Yield Lever (6V Engine)Fig. 5 - Adjusting Throttle Delay CylinderFig. 6 - Typical Variable Speed Governor Lever PositionFig. 7 . Typical Limiting Speed Governor Lever PositionFig. 1 - Hydraulic Governor Mounted on EngineFig. 3 - Adjusting Length of Fuel RodFig. 5 - Adjusting Maximum Engine SpeedFig. 1 - Hydraulic Governor MountingFig. 1 - Checking Compression PressureEngine Out of FuelCrankcase PressureAir Box PressureFig. 2 - Comparison of Column Height for Mercury and Water ManometersPREPARING ENGINE FOR STORAGETURBOCHARGERPROCEDURE FOR RESTORING AN ENGINE TO SERVICE WHICH HAS BEEN IN EXTENDED STORAGEHYDROSTARTERBuilt-In Parts BookBuilt-In Parts Book - ContinuedBuilt-In Parts Book - ContinuedBuilt-In Parts Book - ContinuedBuilt-In Parts Book - ContinuedBuilt-In Parts Book - ContinuedBuilt-In Parts Book - ContinuedCONNECTING ROD, PISTON AND LINERACCESSORY DRIVE FOR DIRECT DRIVEN ACCESSORY (CAMSHAFT GEAR)VALVE OPERATING MECHANISM (4 VALVE)TYPICAL FUEL OIL STRAINERAIR SHUT-DOWN HOUSINGBLOWER ASSEMBLY AND DRIVE (4 CYL.)BLOWER ASSEMBLY AND DRIVE (6 CYL.)OIL PUMP AND REGULATOROIL FILTEROIL COLLER (6V-53)FRESH WATER PUMPFAN MOUNT (6V-53)FAN MOUNTWATER TEMPERATURE SHUTDOWN SWITCHTACHOMETER DRIVE COVERS AND ADAPTORSAIR COMPRESSOR AND DRIVEOWNER ASSISTANCEOWNER ASSISTANCE - ContinuedALPHABETICAL INDEXALPHABETICAL INDEX - ContinuedENGLISH TO METRIC CONVERSIONSService ManualFOREWORDTABLE OF CONTENTSSCOPE AND USE OF THE MANUALPRINCIPLES OF OPERATIONGENERAL DESCRIPTIONFig. 2 - In-line Engine Model Description, Rotation, and Accessory ArrangementsFig. 3 - 6 and 8V Engine Model Description, Rotation and Accessory ArrangementsFig. 4 - Cylinder Designation and Firing OrderFig. 5 - Typical Model and Serial Numbers as Stamped on Cylinder Block (In-Line Engine)GENERAL PROCEDURESRust PreventiveWORK SAFELYCross Sections of a Typical In-Line EngineSECTION 1. ENGINE (less major assemblies)Fig. 1 - Cylinder Block (Four Cylinder Block Shown)Fig. 3 - Air and Water Passages in In-Line Cylinder BlockRemove and Disassemble EngineFig. 6 - Cylinder Head Gaskets and Seals in Place on Cylinder BlockFig. 8 - Vertical Oil Passages in Top of Cylinder BlockFig. 11 - Location of Block Bore Seal Ring GrooveFig. 14 - Typical Cylinder Block MarkingsInspect Cylinder BlockAssemble and Install EngineFig. 1 - Cylinder Block Rear End Plate Mounting (In-Line Engine)CYLINDER BLOCK END PLATEFig .1 Air Box Drain Tube Mounting (In-Line Engines)InspectionFig. 1 - Typical Four-Valve Cylinder Head AssemblyCylinder Head MaintenanceDisassemble Cylinder HeadFig. 3 - Checking Bottom Face of Cylinder Head for WarpageFig. 5 - Correct Installation of Water Nozzles in Four-Valve Cylinder HeadFig. 6 - Sequence for Tightening Cylinder Head BoltsInstall Cylinder HeadVALVE AND INJECTOR OPERATING MECHANISMFig. 3 - Removing Push Rod from Upper Side of Cylinder Head with Tool J 3092-01Remove Cam Follower and Push Rod Assembly (Cylinder Head Not Removed from Engine)Fig. 7 - Removing or Installing Cam Follower Roller and Pin with Tool J 5840Fig. 10 Adjusting Cam-Follower GuideFig. 11 - Push Rod Spring IdentificationFig. 12 - Relationship Between Exhaust Valve Bridge and Valve StemsInstall Rocker Arms and Rocker Arm ShaftEXHAUST VALVESRemove Exhaust Valve Spring (Cylinder Head Installed)InspectionFig. 5 - Removing Valve GuideFig. 7 - Removing Valve Seat InsertFig. 9 - Refacing Exhaust ValveFig. 12 - Relationship Between Exhaust Valve, Insert and Cylinder Head (4 Valve Head)Fig. 14 - Checking Relative Concentricity of Valve Seat Insert with Relation to Valve GuideFig. 16 - Checking Valve Opening Pressure with Gage WRE-500-60Fig. 1 - Typical Valve Rocker Cover AssemblyFig. 1 - Crankshaft Details and Relative Location of Parts (Three Cylinder In-Line Engine Crankshaft Shown)Fig. 3 - Removing or Installing CrankshaftFig. 4 - Typical Ridging of CrankshaftFig. 6 - Crankshaft Fatigue CracksFig. 7 - Dimensions of Crankshaft Journals - In-Line EngineCrankshaft GrindingFig. 10 - Standard Dimensions at Crankshaft Thrust Surfaces--in-Line EnginesInstall CrankshaftCRANKSHAFT OIL SEALSFig. 3 - Use of Rear Oil Seal Sleeve on Grooved Crankshaft (In-Line Engines)Install Crankshaft Front Oil SealInstall Crankshaft Rear Oil SealFig. 1 - Main Bearing Shells, Bearing Caps and Crankshaft Thrust Washers -- In-Line EnginesFig. 4 - Removing Upper Main Bearing Shell (Except Rear Main)Fig. 6 - Comparison of Main Bearing ShellsFig. 7 - Main Bearing MeasurementsFig. 9 - Crankshaft Thrust Washers in PlaceInstall Main Bearing Shells (Crankshaft in Place)Fig. 1 - Engine Front Cover Mounting (Lower) -- In-Line EngineFig. 3 - Installing Lower Engine Front Cover -- In-Line EngineCRANKSHAFT PULLEYFig. 3 - Cone Mounted PulleyFig. 1 - Removing FlywheelInstall Ring GearFLYWHEEL HOUSINGFig. 3 -Flywheel Housing Bolt Sizes and Tightening Sequence (Operation 1)--In-Line EngineFig. 6 - Flywheel Housing Bolt Tightening Sequence (Operation 2)--In-Line EngineFig. 9 Checking Flywheel Housing ConcentricityInstall Flywheel HousingPISTON AND PISTON RINGSFig. 3 - Cleaning PistonFig 4 - Comparison of PistonsFig. 5 - Removing or Installing Piston Pin BushingsFig. 8 - Measuring Piston-to-liner ClearanceFitting Piston RingsOIL CONTROL RINGSFig. 1 - Connecting Rod MountingFig. 3 - Magnetic Particle Inspection Limits for Connecting RodFig. 4 - Removing or Installing BushingsFig. 8 - Reaming BushingsAssemble Connecting Rod to PistonCONNECTING ROD BEARINGSInstall Connecting Rod Bearing ShellsFig. 1 Cylinder LinerFig. 4 - Checking Bore of Cylinder LinerFig. 6 Cylinder Liner Ridge Due to WearFig. 7 - Checking Distance of Liner Flange Below Top Face of BlockFig 9. - Cylinder Liner Seal ring Location in Cylinder Block BoreInstall Cylinder Liner, Piston and Connecting Rod AssemblyENGINE BALANCE AND BALANCE WEIGHTSInstall Front Balance WeightsGEAR TRAIN AND ENGINE TIMINGGEAR TRAIN AND ENGINE TIMING - ContinuedGEAR TRAIN AND ENGINE TIMING - ContinuedENGINE TIMINGENGINE TIMING - ContinuedFigure 1. Removing or Installing Nut on Camshaft or Balance ShaftFigure 3. Removing End BearingFigure 4. Installing Intermediate Camshaft BearingFigure 5. Camshaft and Balance Shaft Bearing IdentificationInstall End BearingsFigure 7. Removing and Replacing Camshaft or Balance Shaft BearingsFigure 8. Camshaft and Balance Shaft Details and Relative Location of PartsCAMSHAFT AND BALANCE SHAFT GEARSFigure 2. Installing Camshaft GearFigure 1. Installing Idler Gear HubFigure 3. Idler Gear Details and Relative Location of PartsFigure 1. Removing Crankshaft Timing GearInstall Crankshaft Timing GearFigure 1. Accessory Drive Locations (In Line Engines)Figure 3. Air Compressor DriveFigure 5. Components of Accessory Drive for Belt Driven Accessory (Drive Hub Type)Figure 7. Former and Current Drive Plate Type Accessory DriveInstall Accessory DriveENGINE FRONT COVER ( UPPER )Install CoverFig. 1 - Using Plastic Strip to Measure Bearing-to-Crankshaft ClearanceCAMSHAFT CUP PLUG INSTALLATIONTROUBLE SHOOTINGSPECIFICATIONSTABLE OF SPECIFICATIONS, NEW CLEARANCE AND WEAR LIMITSTABLE OF SPECIFICATIONS, NEW CLEARANCE AND WEAR LIMITS - ContinuedTABLE OF SPECIFICATIONS, NEW CLEARANCE AND WEAR LIMITS - ContinuedEXCEPTIONS TO STANDARD BOLT AND NUT TORQUE SPECIFICATIONSSTANDARD PIPE PLUG TORQUE SPECIFICATIONSTOOL NAMETOOL NAME - ContinuedSECTION 2. FUELS SYSTEM AND GOVERNORSFig. 1 Typical Fuel System for In- Line EnginesFig. 1 Fuel Injector AssemblyFig. 4 Phases of Injector Operation Through Vertical Travel of PlungerFig. 6 Fuel Injector MountingFig. 8 Checking Rack and Plunger for Free MovementFig. 10 Spray Pattern TestINJECTOR CONTROL RACK AND PLUNGER MOVEMENT TESTINJECTOR HIGH PRESSURE TESTFig. 14 Injector Needle Valve Test with Auxiliary Test J 22640Fig. 17. Placing Injector in Comparator J 7041Fig 20. Position of Calibrator Fuel Flow PipesFig. 21. Injector in Calibrator J 224410Fig. 24. Removing or Installing Plunger Follower, Plunger and SpringFig. 26. Removing Spray Tip Injector NutClean Injector PartsFig. 33. Lapping Spray Tip on Lapping Blocks J 22090Fig. 35. Details of Injector Filters and Caps and Their Relative LocationFIG. 38. Comparison of former and New Design Injector PartsLapping Injector PartsASSEMBLE PLUNGER AND FOLLOWERTest Reconditioned InjectorFUEL INJECTOR TUBEFig. 3 Upsetting Injector TubeFig. 5 - Reaming Injector Tube for Injector NutFig. 1. Typical Fuel Pump AssemblyFig. 2. Fuel Pump Valving and Rotation (Right Hand Pump Shown)Fig. 4. Removing Oil SealsFig. 5 Fuel Pump Details and Relative Location of Parts ( Right Hand Pump Shown)Fig. 7. Installing Outer Oil SealFUEL PUMP DRIVEMECHANICAL GOVERNORSLIMITING SPEED MECHANICAL GOVERNORFig. 2 Governor Cover Details and Relative Location of PartsFig. 4 Removing Fork from Operating ShaftInspectionFig. 5 - Governor Housings and Relative Location of PartsInstall GovernorInstall Governor - ContinuedSHOP NOTES-TROUBLE SHOOTING-SPECIFICATIONS-SERVICE TOOLSFig. 2 - Injector Rack-to-Gear TimingFig. 3 - Checking Fuel OutputFig. 4. Types of Injector PlungersLOCATING AIR LEAKS IN FUEL LINESTROUBLE SHOOTING CHARTS (Needle Valve Injectors)TROUBLE SHOOTING CHARTS (Needle Valve Injectors) - ContinuedTROUBLE SHOOTING CHARTS (Needle Valve Injectors) - ContinuedFUEL PUMP MAINTENANCESPECIFICATIONSSERVICE TOOLSSECTION 3. AIR INTAKE SYSTEMFig. 1 - Air Silencer Mounted on In-Line EngineFig. 1 - Typical In - Line Air Shut Down Housing Details and Relative Location Of PartsFig. 3 - Location of Air Shut-Down Housing Mounting Bolts (In-Line Engines)Install Air Shut-Down Housing (In-Line Engines)Fig. 1 - Blower Mounting (3-53 Engine)Fig. 5 Removing Blower Rotor GearsDisassemble BlowerFig. 7 - Typical Blower Details and Relative Location of Parts (3-53 Engine Blower)Fig. 9 - Installing Lip Type Oil Seal in End PlateFig. 13 - Installing Blower Rotor GearsFig. 15- Minimum Blower Rotor ClearanceFig. 16 - Measuring Rotor Lobe to End Plate ClearanceFig. 17 - Inserting Cam in Blower Drive SupportENGINE BLOWERSHOP NOTES - TROUBLE SHOOTING - SPECIFICATIONS - SERVICE TOOLSFig. 3 - Positioning Cutting Tool in Fixture GuideTABLE OF SPECIFICATIONS, NEW CLEARANCES AND WEAR LIMITSEXCEPTIONS TO STANDARD BOLT AND NUT TORQUE SPECIFICATIONSSERVICE TOOLSSECTION 4. LUBRICATION SYSTEMFig. 1 - Schematic Diagram of typical In-Line Engine Lubrication System,Lubricating Oil DistributionCleaning Lubrication SystemFig. 1 - Typical Right - Hand Rotation Lubricating Oil Pump MountingFig. 3 - Measuring Rotor ClearanceFig. 5 - Lubricating Oil Pump Details and Relative Location of Parts (Current)Fig. 7 - Removing Oil Pump Drive Gear pump body. Since the holes are offset, the cover plateInstall Oil PumpLUBRICATING OIL PRESSURE REGULATORFig. 1 Typical Oil Cooler Mounting (6V-53 Engine Shown)Fig 3 - Oil Cooler Details and Relative Location of Parts (In-Line Engine)Pressure Check Oil Cooler CoreInstall Oil Cooler CoreFig. 1 - Typical Oil Dipstick MountingRemoving and Installing Oil PanFig. 1 - Typical Crankcase Breather Mounting (In-Line Engine)VENTILATING SYSTEMSPECIFICATIONS - SERVICE TOOLSSTANDARD BOLT AND NUT TORQUE SPECIFICATIONSSECTION 5. COOLING SYSTEMWATER PUMPFig. 3 - Removing PulleyFig. 6. Fresh Water Pump Details and Relative Location of PartsFig. 7 - Comparison of Water PumpsFig. 2. Thermostat Housing Details and Relative Location of Parts (In-Line Engine)Fig. 4. Method of Checking Thermostat OperationFig. 5. Bleed Hole in Thermostat HousingENGINE COOLING FANFig. 3. Removing Fan Hub (Pulley)Fig. 5 - Current Fan Hub Assembly (In-Line Engine)Fig. 8. Typical Fan Hub and Adjusting Bracket Details and Relative Location of Parts (In-Line Engine)IN-LINE ENGINES (CURRENT)Install Fan, Hub and Adjusting BracketWATER FILTER AND CONDITIONERWATER FILTER AND CONDITIONER - ContinuedSTANDARD BOLT AND NUT TORQUE SPECIFICATIONSSECTION 6. EXHAUST SYSTEMEXHAUST MANIFOLD (AIR COOLED)Install Exhaust ManifoldSECTION 7. ELECTRICAL EQUIPMENT, INSTRUMENTS AND PROTECTIVEBATTERY-CHARGING GENERATOR (D.C. AND A.C.)Fig. 2 - 30 DN Type 100 A.C. Self-Rectifying Generator (Alternator)Alternator PrecautionsFig. 4. 20 DN Type 250 A.C. Self-Rectifying Generator (Alternator)BATTERY-CHARGING GENERATOR REGULATORTRANSISTORIZED AND TRANSISTOR REGULATORSTRANSISTOR REGULATORFig. 5 - Transistor Regulator with Plug-In ConnectionsSTARTING MOTORFig. 2 - Cross-Section of Motor with Intermediate-Duty ClutchRemove Starting MotorSPECIFICATIONS - SERVICE TOOLSCHECKING ENGINE ELECTRICAL GENERATING SYSTEMSERVICE TOOLSSECTION 13. OPERATION INSTRUCTIONSENGINE OPERATION INSTRUCTIONSStorage BatteryOil PressureEmergency StoppingENGINE OPERATING CONDITIONS3-53 IN-LINE ENGINE (4-Valve Cylinder Head)3-53 IN-LINE ENGINE (4-Valve Cylinder Head) - ContinuedENGINE RUN-IN INSTRUCTIONSInstrumentationBASIC ENGINE RUN-INENGINE TEST REPORTINSPECTION AFTER FINAL RUN-INDETROIT DIESEL FUEL OIL SPECIFICATIONSDETROIT DIESEL LUBRICATING OIL SPECIFICATIONSENGINE COOLANTINHIBITOR SYSTEMSCOOLANT INHIBITOR CHARTANTIFREEZECOOLANT RECOMMENDATIONSSECTION 14. ENGINE TUNE UPEXHAUST VALUE CLEARANCE ADJUSTMENTEXHAUST VALUE CLEARANCE ADJUSTMENTFig. 2 - Adjusting Valve Clearance (Four Valve Head)Fig. 1 - Timing Fuel InjectorFig. 1 - Adjusting Governor GapFig. 2 - Positioning the Rear Injector Rack Control LeverFig. 3 - Adjusting Maximum No-Load Engine SpeedFig. 5 - Adjusting Engine Idle SpeedSECTION 15. PREVENTIVE MAINTENANCE - TROUBLE SHOOTING - STORAGELUBRICATION AND PREVENTIVE MAINTENANCELUBRICATION AND PREVENTIVE MAINTENANCE CHARTLUBRICATION AND PREVENTIVE MAINTENANCE - ContinuedLUBRICATION AND PREVENTIVE MAINTENANCE - ContinuedLUBRICATION AND PREVENTIVE MAINTENANCE - ContinuedLUBRICATION AND PREVENTIVE MAINTENANCE - ContinuedLUBRICATION AND PREVENTIVE MAINTENANCE - ContinuedLUBRICATION AND PREVENTIVE MAINTENANCE - ContinuedLUBRICATION AND PREVENTIVE MAINTENANCE - ContinuedLUBRICATION AND PREVENTIVE MAINTENANCE - ContinuedExhaust Back PressureFig. 2 - Comparison of Column Height for Mercury and Water ManometersTrouble Shooting (Engine)Trouble Shooting (Engine) - ContinuedTrouble Shooting (Engine) - ContinuedTrouble Shooting (Engine) - ContinuedTrouble Shooting (Engine) - ContinuedTrouble Shooting (Engine) - ContinuedTrouble Shooting (Engine) - ContinuedTrouble Shooting (Engine) - ContinuedTrouble Shooting (Engine) - ContinuedTrouble Shooting (Engine) - ContinuedTrouble Shooting (Engine) - ContinuedTrouble Shooting (Engine) - ContinuedSTORAGEEXTENDED STORAGE (30 days or more)PROCEDURE FOR RESTORING AN ENGINE TO SERVICE WHICH HAS BEEN IN EXTENDED STORAGEALPHABETICAL INDEXALPHABETICAL INDEX - ContinuedALPHABETICAL INDEX - ContinuedPART III. ENGINE PARTS MANUALGROUP NOMENCLATUREGROUP NOMENCLATURE - ContinuedGENERAL INFORMATIONALPHABETICAL INDEXALPHABETICAL INDEX - ContinuedALPHABETICAL INDEX - ContinuedALPHABETICAL INDEX - ContinuedALPHABETICAL INDEX - ContinuedALPHABETICAL INDEX - ContinuedALPHABETICAL INDEX - ContinuedALPHABETICAL INDEX - ContinuedALPHABETICAL INDEX - ContinuedALPHABETICAL INDEX - ContinuedALPHABETICAL INDEX - ContinuedINDEXMODEL DESCRIPTION CHART IN-LINE ENGINESFIG. 1A INLIE 53 CYLINDER BLOCK (with head gasket)FIGURE 2A. CYLINDER HEADFIGURE 3A. CRANKSHAFT (3-53)fIG. 4D. LOWER FRONT COVER AND OIL PUMPFIG. 5A. FLYWHEEL AND FLYWHEEL HOUSING (In-Line Models)FIG. 6A. CONNECTING ROD, PISTON AND LINERFIG. 7A. CAMSHAFT (In-Line Models)FIG. 7C. GEAR TRAIN (Typical In-Line)FIG. 8A. ACCESSORY DRIVE (Double Bell)FIG. 9A. VALVE MECHANISMROCKER COVERTYPICAL 4 CYLINDER FAN TO FLYWHEEL INDUSTRIAL UNITBLOCK ASSY., CYLINDERBLOCK CYLINDERHEAD ASSY. CYLINDERCOVER, CYLINDER HEAD WATER HOLEHEAD ASSEMBLY, CYLINDERCRANKSHAFT ASSYSHELL, CRANKSHAFT MAIN BEARINGCOVER, ENGINE FRONT-LOWERFLYWHEELHOUSING, FLYWHEELCONNECTING ROD ASSYPISTON ASSYCYLINDER KITBEARING, CAM AND BALANCER SHAFTWEIGHT, REAR BALANCERADAPTOR, ACCESSORY DRIVEARM ASSY. EXHAUST VALVEBRACKET, ROCKER SHAFTVALVE, EXHAUSTGASKET, ROCKER COVERGROUP NOMENCLATUREFIG. 1B. FUEL INJECTORFIG. 2B. FUEL PUMP DRIVEFIG. 3B. FUEL FILTER (Canister Type Element)FIG. 4A. TYPICAL FUEL SYSTEM (In-Line Engine)FIG. 5D. MECHANICAL GOVERNOR HOUSING WEIGHTS AND LEVER (Closed Linkage)INDUSTRIAL TYPEFIG. 5H. MECHANICAL GOVERNOR COVER (Double Lever)FIG. 5L. GOVERNOR WEIGHT SHAFT AND CARRIERFigs. 7A of 2.0000INJECTOR ASSYSPRING, INJECTOR PLUNGERRETAINER, INJECTOR GEARPUMP ASSY., FUELSEAL, FUEL PUMP OILGASKET, FUEL PUMP TO ENGINESPRING, FUEL PUMP VALVE RETAININGSTRAINER ASSY., FUELPLUG, FUEL STRAINER COVERGASKET, FUEL FILTER COVER TO SHELLPIPE, FUELVALVE, FUEL SUPPLY CHECKGOVERNOR ASSYLEVER, GOVERNOR COVER THROTTLE SHAFTLEVER, GOV. OPERATING SHAFTSPRING, GOVERNOR LOW SPEEDSCREW ASSY., GOV. BUFFERSEAL, GOVERNORSHAFT, GOVERNOR WEIGHT CARRIERSUPPORT, GOVERNOR WEIGHT SHAFT BEARINGBRACKET, INJECTOR CONTROL TUBEPIN, GOVERNOR CONTROL WIRE SWIVELGROUP NOMENCLATUREFIG. 3A. AIR INLET HOUSINGFIG. 4A. 3-53. BLOWERHOUSING ASS ., AIR INIETWIRE, AIR INIET HOUSING SHUTDOWNBLOWER ASSYSCREEN, BLOWERSEAL, BLOWER HOUSING END PLATEGROUP NOMENCLATUREFIG. 1A. OIL PUMP AND PRESSURE REGULATOR (Inline Engine)FIG. 2A. OIL DISTRIBUTION SYSTEMFIG. 3A. OIL FILTERFIG. 4C. OIL COOLERFIG. 6A. DIPSTICKFIG. 7B. OIL PAN (STAMPED)FIG. 8A. BREATHER AND OIL FILLERPUMP ASSY., OILVALVE, OIL PRESSURE REGULATORFILTER ASSY., OILGASKET, OIL FILTER COVER NUTGASKET, OIL FILTER TUBE ADAPTORCORE ASSY., OIL COOLERCAP, OIL FILLER TUBEDIPSTICKPAN, OILPIPE, BREATHERGROUP NOMENCLATUREFIG. 1A. TYPICAL COOLING SYSTEM (Inline Engines)FIG. 2A. FRESH WATER PUMPPUMP ASSY., FRESH WATERGASKET, FRESH WATER PUMP- BODY COVERELBOW, WATER OUTLETHOSE, WATER BY-PASS TUBEELBOW, OIL COOLER WATER OUTLETBLADE, FANSEAL, FAN SHAFTGROUP NOMENCLATUREFIG. 1A. EXHAUST MANIFOLD (Center Outlet)MANIFOLD, EXHAUSTFLANGE, EXHAUSTGROUP NOMENCLATUREFIG. 1A. BATTERY CHARGING GENERATORGENERATOR ASSYBRACKET, GENERATOR MOUNTINGMOTOR ASSY., STARTING
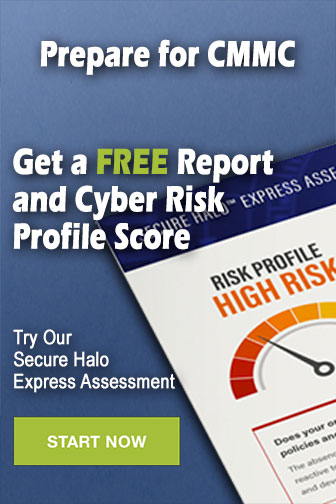